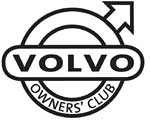
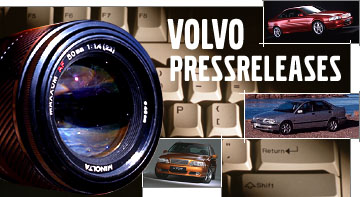
Photographs can be seen in our Volvo Gallery
Volvo V50 SV Features Full Compliment of Swedish Manufacturer's Renowned Safety Systems
2 November 2004
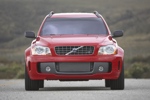

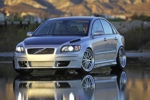
Las Vegas, Nevada (November 2, 2004) - The Volvo V50 SV, making its debut today at the 2004 Specialty Equipment Manufacturers Association tradeshow, features an array of safety systems designed and developed in the world's most state of the art Safety Center in Gothenburg, Sweden. "The Volvo V50 SV, while highly modified, wouldn't be a Volvo without its full complement of safety systems," said Thomas Andersson, Executive Vice President of Marketing at Volvo Cars of North America, LLC.
To that end, the Volvo V50 SV comes standard with a myriad of safety systems including antilock brakes with brake force distribution, the Volvo Side Impact Protection System (SIPS), Volvo's Whiplash Protection System (WHIPS) and the new patented front structure that incorporates four different grades of steel. It's all part of Volvo's Intelligent Vehicle Architecture (VIVA), a unique approach to building a car that integrates everything from its crashworthiness, to its dynamic styling and exciting driving characteristics.
The safety systems have been developed and tested in the Volvo Cars Safety Center, the most advanced facility of its kind in the world. About forty full-scale tests have been performed to help ensure that all the on-board components interact, not to mention an untold number of computer crash simulations.
During the development of the new Volvo V50, the goal was to achieve class-leading safety utilizing a new way of thinking about how cars deform in the event of a collision.
"Our aim of building cars that are the safest in their class applies to all models, including the new Volvo V50," says Ingrid Skogsmo, head of the Volvo Cars Safety Centre.
In a collision, the preconditions for efficient deformation are critical. Since the necessary deformation is absorbed within a limited total distance, the various materials’ properties must be exploited to the maximum so as to absorb as much of the incoming energy as possible.
"A tough challenge, but one that we approached in an entirely new way," confirms Ingrid Skogsmo. "We call it Volvo's Intelligent Vehicle Architecture."
The frontal body structure of the new Volvo V50 is divided into several zones, each with a different task in the deformation process. The outer zones are responsible for most of the deformation. The closer the collision forces get to the passenger compartment, the less the materials used deform. The intention is that the passenger compartment should remain intact in most collisions.
In order to give each zone the relevant properties, different grades of steel are used in different areas. Four different steel grades are used. In addition to conventional bodywork steel, three different grades of high-strength steel are employed: High Strength Steel, Extra High Strength Steel and Ultra High Strength Steel.
What's also unique is that the all-new V50 went through a series of computer simulated frontal crash tests without the installed engine. The engines were then designed to fit within the empty space that remained after the simulated crash test. In a real collision the engine may be shunted reward 5.9 inches before contacting the bulkhead.
This zonal system enables the collision forces to be absorbed in a highly ingenious and effective manner:
Low-speed deformation zone
The front
bumper incorporates an extremely rigid crossmember of boron steel. The
attachments to the longitudinal members of the body are designed in the form of
‘crash boxes’, which absorb the forces generated by a low-speed
collision without damage to the rest of the body structure. The crash boxes can
be replaced easily at reasonable cost.
High-speed deformation zone
The
straight sections of the side members are made of high strength steel, a very
ductile grade of material, which is optimized for high-energy absorption. This
zone accounts for most of the deformation in a collision. In addition, Volvo
has opted to include upper side cross-members since they provide essential
protection if the vehicle should collide, for example, with a truck platform or
a loading pier.
Back-up zone
The section of cross-member
that turns outward toward the A-pillar is designed to act as a barrier
protecting the cabin space and as a back-up against deformation. The design
also helps minimize the possibility of the front wheel from penetrating the
interior, the wheel instead helping to absorb the collision forces. This
section is extremely rigid and is made of extra high-strength steel.
Three-way attachment
A rigid
cross-member connects the A-pillars and lower side members. On each side they
form an extremely rigid three-way attachment, which helps to preserve the
passenger compartment. The new front structure is one of Volvo’s many
patented safety designs, and is an important part of Volvo's Intelligent
Vehicle Architecture
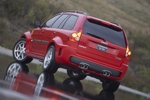
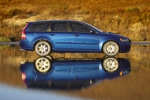
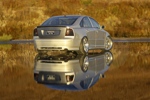
Legal | Privacy | Contact Us | Search | Site Map
Volvo Owners' Club Limited® 1962-2025